Table of Contents
- Introduction
- The Role of Solid Carbide Cutting Tools in Green Manufacturing
- Advantages of Solid Carbide Cutting Tools
- Durability and Longevity
- Improved Efficiency
- Material Conservation
- Environmental Impact Reduction
- Energy Savings
- Reduced Emissions
- Waste Management
- Case Studies and Real-World Applications
- Automotive Industry
- Aerospace Industry
- Medical Device Manufacturing
- Technological Advancements in Solid Carbide Cutting Tools
- Coatings and Surface Treatments
- Innovations in Tool Design
- Sustainable Practices in Manufacturing
- Lean Manufacturing
- Circular Economy Principles
- Challenges and Solutions in Adopting Solid Carbide Cutting Tools
- Initial Costs and Investment
- Training and Skill Development
- Future Trends in Green Manufacturing
- Industry 4.0 and Digitalization
- Renewable Energy Integration
- Conclusion
Introduction
Solid Carbide Cutting Tools are becoming a pivotal element in the push towards greener manufacturing. As industries worldwide strive to reduce their environmental footprint, the adoption of these advanced tools is leading to significant improvements in efficiency and sustainability. This comprehensive guide explores the various ways in which solid carbide cutting tools contribute to a more sustainable manufacturing process, examining their advantages, environmental impacts, and real-world applications.
The Role of Solid Carbide Cutting Tools in Green Manufacturing
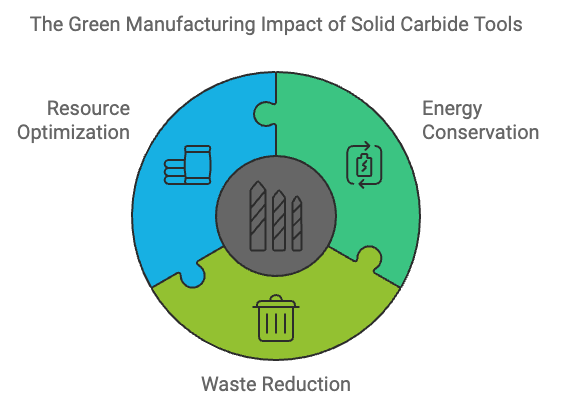
Solid carbide cutting tools are designed to perform at high speeds and with high precision, leading to less waste and more efficient use of materials. This efficiency not only enhances production but also contributes to environmental sustainability. The role of these tools in green manufacturing is multifaceted, encompassing aspects of energy conservation, waste reduction, and resource optimization.
Solid carbide cutting tools stand out for their ability to maintain performance under demanding conditions. This reliability reduces the need for frequent replacements, which in turn minimizes waste. Additionally, their high-speed capabilities ensure that manufacturing processes are completed faster, resulting in lower energy consumption.
Advantages of Solid Carbide Cutting Tools
1. Durability and Longevity
Solid carbide cutting tools are renowned for their exceptional durability. Their long lifespan means fewer replacements, resulting in less waste and reduced resource consumption. This durability is achieved through the use of high-quality carbide materials, which are known for their hardness and wear resistance.
By lasting longer than traditional tools, solid carbide cutting tools reduce the frequency of tool changes, leading to a decrease in downtime and maintenance costs. This longevity also means that manufacturers can invest in fewer tools over time, further conserving resources and reducing environmental impact.
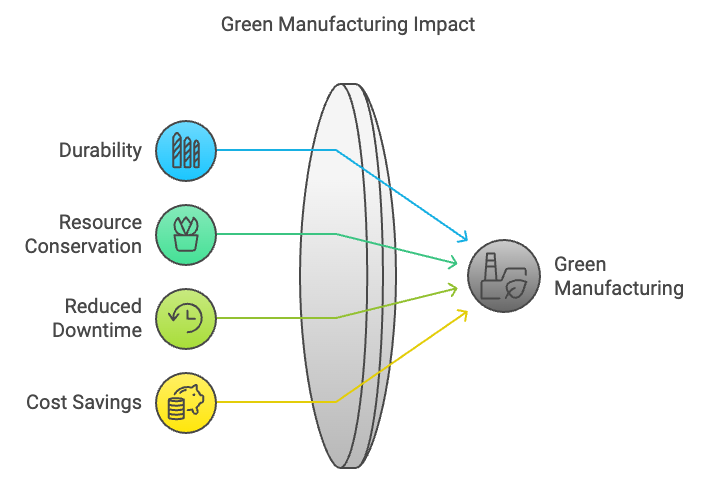
2. Improved Efficiency
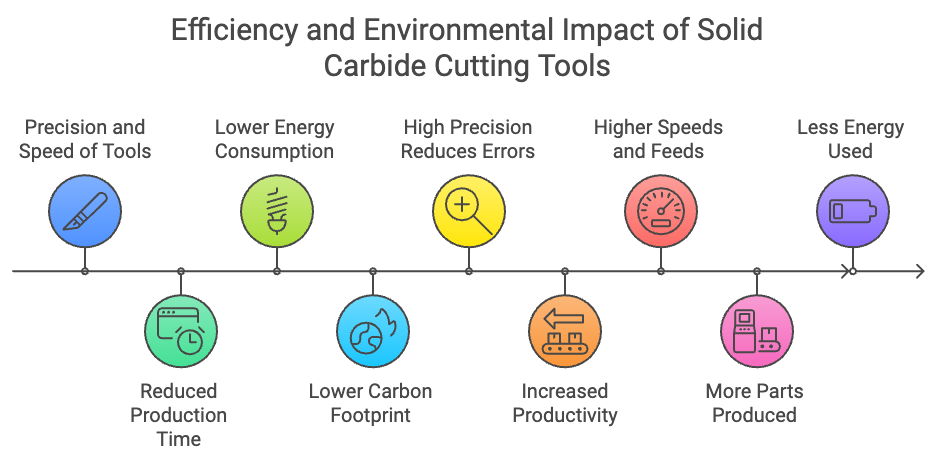
The precision and speed of solid carbide cutting tools reduce production time and energy consumption. This efficiency is a key factor in lowering the overall carbon footprint of manufacturing processes. High precision reduces the likelihood of errors and rework, which can be both time-consuming and resource-intensive.
Efficiency gains are also realized through the ability of solid carbide cutting tools to operate at higher speeds and feeds compared to traditional tools. This increased productivity means that more parts can be produced in a shorter amount of time, using less energy.
3. Material Conservation
These tools produce less waste due to their precision. The reduction in scrap material directly translates to a decrease in the amount of raw material needed, conserving natural resources. Material conservation is particularly important in industries where high-value materials, such as titanium and aerospace alloys, are used.
By minimizing waste, solid carbide cutting tools contribute to a more sustainable manufacturing process. This not only reduces the environmental impact of material extraction and processing but also lowers the cost of raw materials for manufacturers.
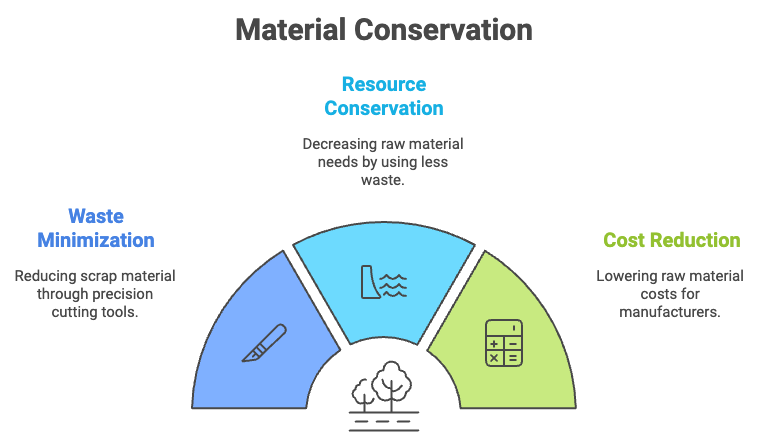
Environmental Impact Reduction
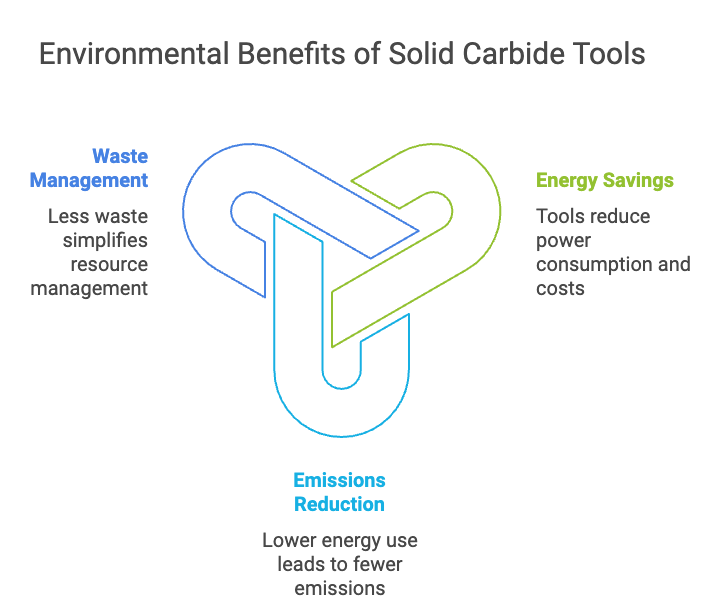
1. Energy Savings
The use of solid carbide cutting tools leads to significant energy savings. Their ability to maintain high speeds and precision means machines run more efficiently, consuming less power. Energy savings are crucial in reducing the overall environmental footprint of manufacturing operations.
Advanced cutting tool technologies, such as those incorporating solid carbide, enable manufacturers to achieve higher material removal rates with less energy input. This efficiency translates into lower electricity bills and reduced greenhouse gas emissions associated with energy production.
2. Reduced Emissions
With lower energy consumption comes a reduction in greenhouse gas emissions. This is crucial for manufacturing facilities aiming to comply with environmental regulations and achieve sustainability goals. By adopting solid carbide cutting tools, manufacturers can significantly reduce their carbon footprint.
Emissions reductions are not limited to direct energy savings. The precision and efficiency of solid carbide cutting tools also lead to fewer defective parts and rework, which can contribute to emissions through the consumption of additional resources and energy.
3. Waste Management
The reduction in waste not only conserves materials but also simplifies waste management processes. This contributes to a cleaner and more sustainable manufacturing environment. Efficient waste management practices are essential for minimizing the environmental impact of manufacturing operations.
By producing less scrap and reducing the need for tool replacements, solid carbide cutting tools help manufacturers streamline their waste management processes. This can lead to cost savings and reduced environmental impact through better resource utilization.
Case Studies and Real-World Applications
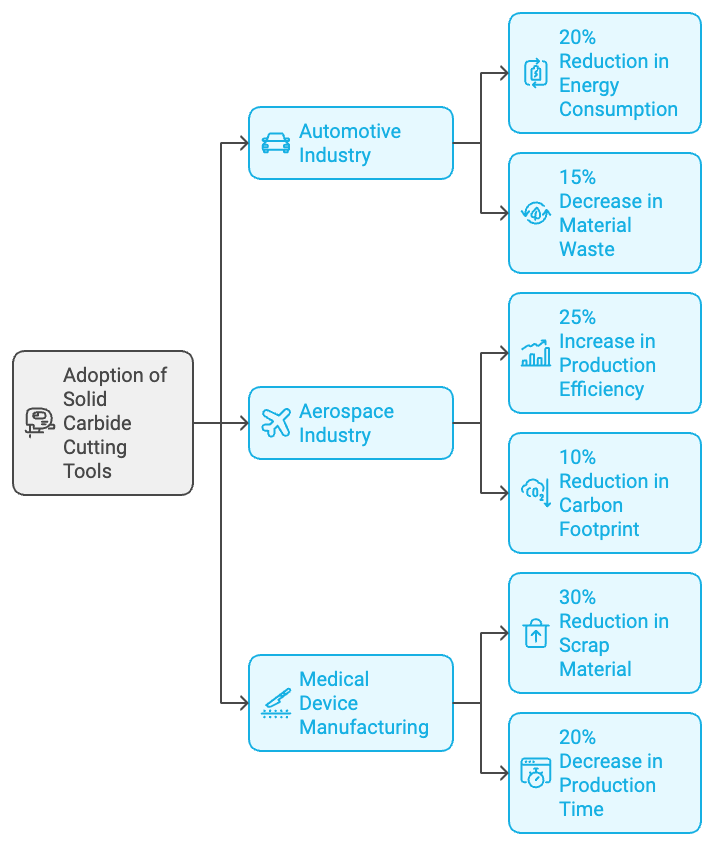
Automotive Industry
In the automotive industry, the use of solid carbide cutting tools has resulted in more precise parts, less material waste, and significant energy savings. This sector has seen a noticeable improvement in its environmental impact through the adoption of these tools.
For example, a leading automotive manufacturer implemented solid carbide cutting tools in their engine production line. The result was a 20% reduction in energy consumption and a 15% decrease in material waste. Additionally, the improved precision of these tools led to higher quality parts and fewer defects.
Aerospace Industry
The aerospace industry benefits from the high precision and durability of solid carbide cutting tools, which are essential for machining high-strength materials like titanium and composite alloys. These tools have enabled aerospace manufacturers to produce parts with tighter tolerances and less waste.
A major aerospace company reported a 25% increase in production efficiency after switching to solid carbide cutting tools. The reduction in waste and energy consumption also contributed to the company’s sustainability goals, helping them achieve a 10% reduction in their overall carbon footprint.
Medical Device Manufacturing
Medical device manufacturers rely on solid carbide cutting tools for their ability to produce intricate and precise components. The high quality and consistency of these tools ensure that medical devices meet stringent regulatory standards while minimizing waste.
A medical device manufacturer adopted solid carbide cutting tools for the production of surgical instruments. This led to a 30% reduction in scrap material and a 20% decrease in production time. The improved efficiency and reduced waste helped the company enhance its sustainability profile.
Technological Advancements in Solid Carbide Cutting Tools
1. Coatings and Surface Treatments
Advancements in coatings and surface treatments have further enhanced the performance and longevity of solid carbide cutting tools. These innovations provide additional wear resistance, reduce friction, and improve heat dissipation, allowing tools to operate at higher speeds and temperatures.
Coatings such as Titanium Nitride (TiN) and Diamond-Like Carbon (DLC) are commonly used to enhance the properties of solid carbide cutting tools. These coatings not only extend the tool’s lifespan but also improve its cutting performance, leading to greater efficiency and sustainability.
2. Innovations in Tool Design
Innovative tool designs have also contributed to the environmental benefits of solid carbide cutting tools. Features such as optimized geometries, advanced chip breakers, and internal cooling channels have improved the performance and efficiency of these tools.
For instance, the development of tools with variable helix angles and pitch has reduced vibration and chatter, resulting in smoother cuts and less wear. Internal cooling channels allow for more effective coolant delivery, reducing the need for excessive coolant use and improving overall machining efficiency.
Sustainable Practices in Manufacturing
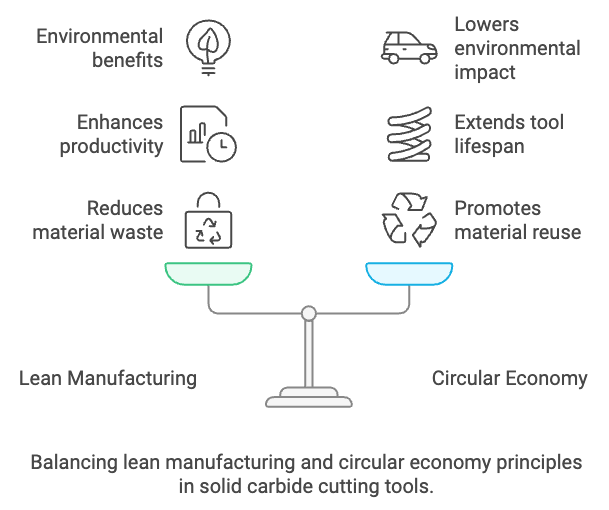
1. Lean Manufacturing
Lean manufacturing principles focus on reducing waste and improving efficiency throughout the production process. Solid carbide cutting tools align well with these principles by minimizing material waste and enhancing productivity.
By incorporating solid carbide cutting tools into lean manufacturing strategies, companies can achieve significant environmental and economic benefits. The reduced waste and improved efficiency contribute to a more sustainable and cost-effective manufacturing process.
2. Circular Economy Principles
The circular economy model emphasizes the importance of resource efficiency and waste reduction by promoting the reuse, recycling, and remanufacturing of products and materials. Solid carbide cutting tools support this model through their durability and extended lifespan.
Manufacturers can further contribute to the circular economy by recycling worn-out solid carbide cutting tools. The carbide material can be reclaimed and reused in the production of new tools, reducing the demand for virgin materials and lowering the environmental impact of tool production.
Challenges and Solutions in Adopting Solid Carbide Cutting Tools
1. Initial Costs and Investment
One of the primary challenges in adopting solid carbide cutting tools is the initial cost and investment required. These tools are typically more expensive than traditional tools, which can be a barrier for some manufacturers.
However, the long-term benefits of solid carbide cutting tools, including their durability and efficiency, often outweigh the initial costs. By reducing waste, energy consumption, and maintenance expenses, these tools can provide significant cost savings over time.
2. Training and Skill Development
Another challenge is the need for training and skill development to effectively use solid carbide cutting tools. Operators and machinists must be trained to optimize tool performance and maximize the benefits of these advanced tools.
Investing in training programs and resources can help manufacturers overcome this challenge. By equipping their workforce with the necessary skills and knowledge, companies can fully leverage the advantages of solid carbide cutting tools and enhance their overall productivity and sustainability.
Future Trends in Green Manufacturing
1. Industry 4.0 and Digitalization
The integration of Industry 4.0 technologies and digitalization is shaping the future of green manufacturing. Advanced data analytics, IoT, and automation are enabling manufacturers to optimize processes, reduce waste, and improve efficiency.
Solid carbide cutting tools are well-suited for these digital advancements. Real-time monitoring and data collection can provide insights into tool performance, enabling predictive maintenance and further enhancing efficiency.
2. Renewable Energy Integration
The integration of renewable energy sources, such as solar and wind power, into manufacturing operations is another trend driving sustainability. By powering their facilities with clean energy, manufacturers can reduce their reliance on fossil fuels and lower their carbon footprint.
The energy savings achieved through the use of solid carbide cutting tools can complement the benefits of renewable energy integration. Together, these strategies can help manufacturers achieve their sustainability goals and reduce their environmental impact.
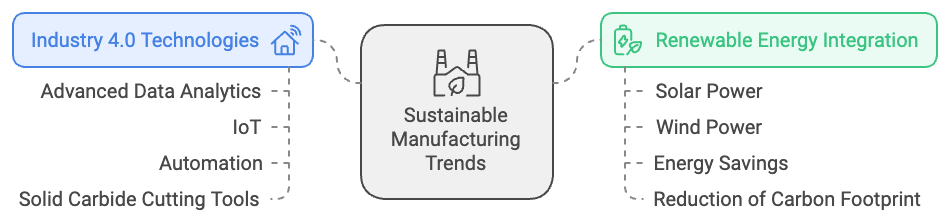
Conclusion
The integration of solid carbide cutting tools into manufacturing processes is a step forward in achieving sustainability. Their durability, efficiency, and precision not only boost productivity but also significantly reduce the environmental impact of manufacturing. By adopting these advanced tools, manufacturers can enhance their sustainability profile, reduce costs, and contribute to a greener future.
Internal Links: