Introduction
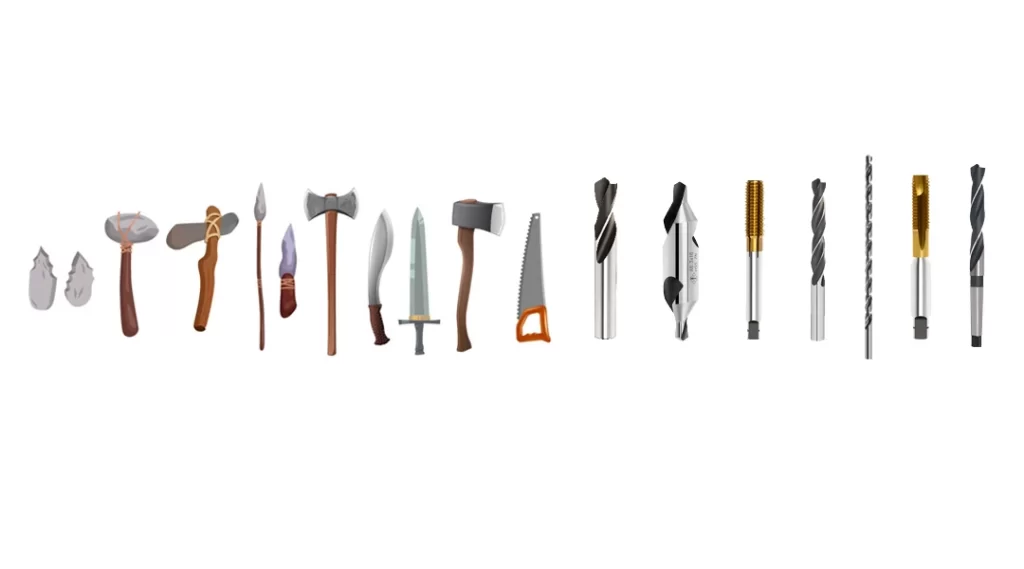
In the realm of modern manufacturing, carbide cutting tools stand out for their exceptional durability, precision, and efficiency. This comprehensive exploration traces the evolution of these indispensable tools, from their humble beginnings to the advanced carbide compositions used today. By dissecting their history, types, and the science behind their success, we’ll uncover why carbide cutting tools have become a cornerstone in a multitude of industries, including aerospace, automotive, and metalworking.
History and Development
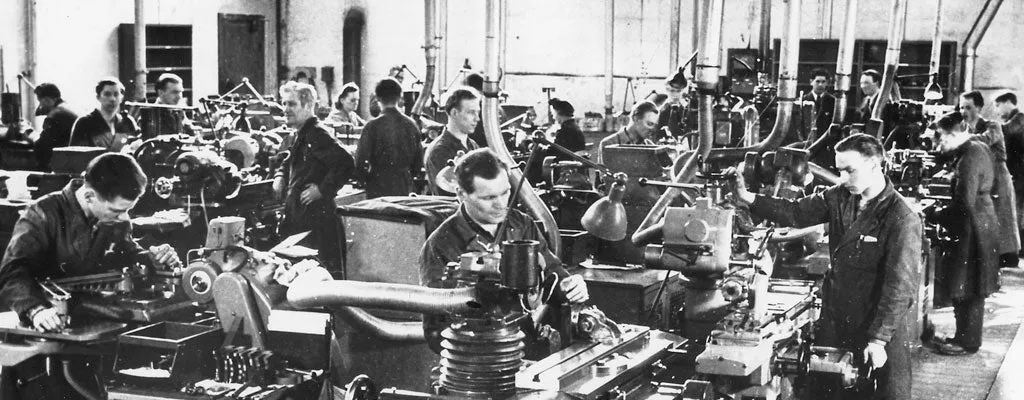
The narrative of carbide cutting tools is a chronicle of innovation and advancement. Initially, the manufacturing sector relied on simpler materials such as steel for cutting tools. However, the incessant quest for more resilient and efficient tools spurred the development of carbides. From the early adoption of basic materials to the breakthrough introduction of tungsten carbide in the 20th century, this section highlights the pivotal technological advancements and milestones that have significantly shaped the evolution of carbide cutting tools.
Types of Carbide Cutting Tools
Carbide cutting tools are categorized into various types, each designed for specific manufacturing tasks. Solid carbide tools, carbide-tipped tools, and carbide inserts are the primary forms, each with its unique applications, benefits, and constraints. This segment delves into the distinctions among these types, providing insights into their suitability for different manufacturing operations.
Material Science Behind Carbide Tools
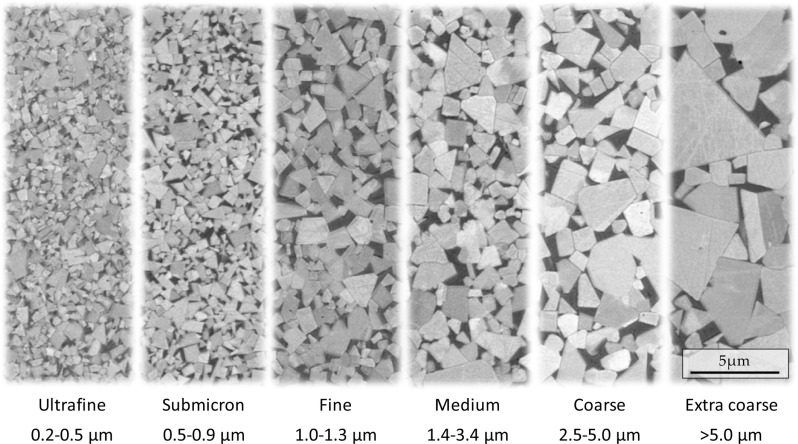
At the heart of carbide tools’ effectiveness is the material science that underpins their design. This section explores the composition and properties of carbide materials, elucidating why they surpass traditional materials in performance. The advantages of carbide tools, such as their hardness, heat resistance, and longevity, are discussed in detail, shedding light on how these attributes translate to superior performance in manufacturing processes.
Manufacturing Processes
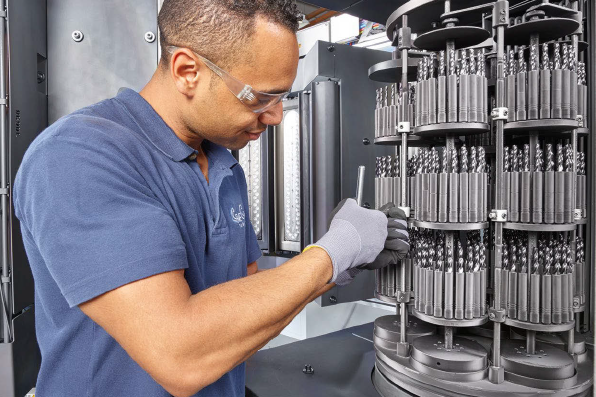
The manufacturing of carbide tools involves intricate processes that significantly impact their quality and performance. From the initial stages of powder metallurgy to the application of advanced coating techniques, this section outlines the comprehensive fabrication process of carbide tools. It also touches on how these manufacturing techniques enhance the tools’ durability and functionality.
Applications in Modern Manufacturing
The versatility of carbide cutting tools allows for their application across a wide range of sectors. This section explores their critical role in aerospace, automotive, and metalworking industries, emphasizing how they meet the high demands for precision and efficiency. The contribution of carbide tools in pushing the boundaries of what’s possible in modern manufacturing is highlighted through various examples.
Advancements in CNC Machining
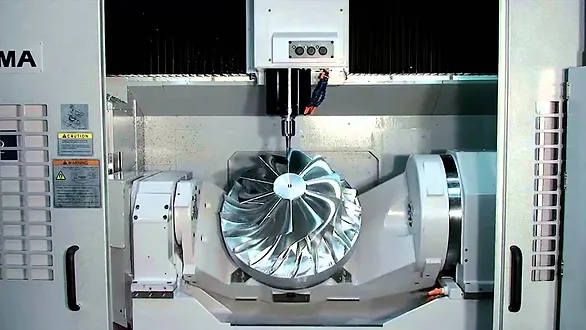
The synergy between carbide cutting tools and CNC (Computer Numerical Control) machining has been a game-changer for the manufacturing industry. This section examines the precision and efficiency achieved through this integration, including the role of CAD/CAM (Computer-Aided Design/Computer-Aided Manufacturing) software in optimizing the use of carbide tools. The advancements in CNC machining facilitated by carbide tools underscore the technological progress in manufacturing.
Impact on Productivity and Cost-Effectiveness
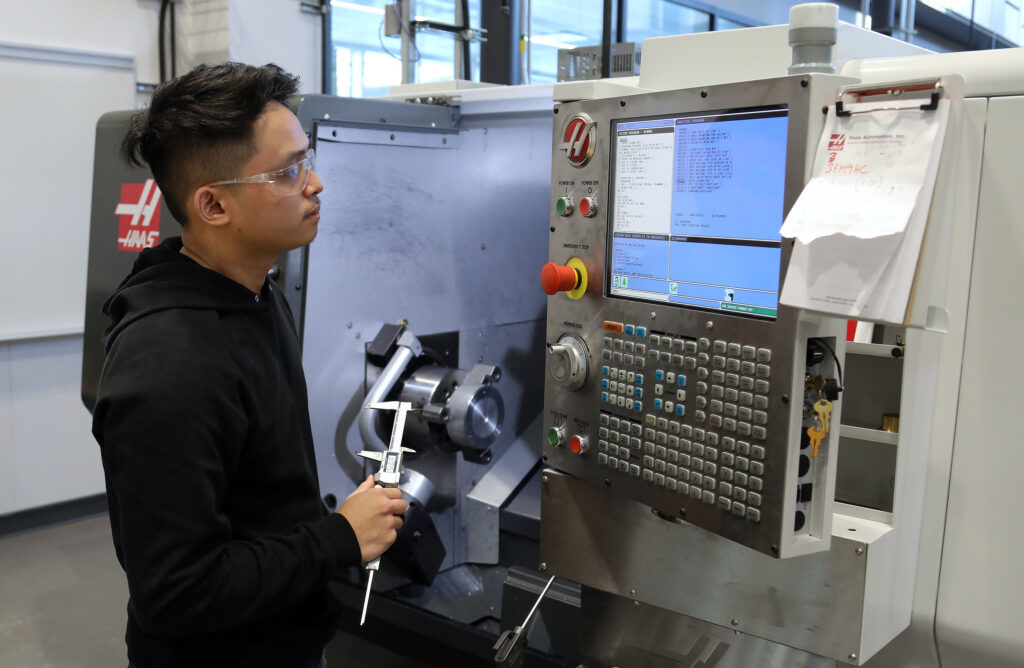
The adoption of carbide cutting tools has markedly influenced productivity and cost-effectiveness in manufacturing. This analysis delves into the economic benefits of using carbide tools, from reducing tool wear to enhancing production speeds. The compelling value proposition offered by carbide cutting tools is discussed, providing insights into how they contribute to more efficient and cost-effective manufacturing processes.
Innovations in Tool Design
Innovation in the design of carbide tools has led to significant improvements in their efficiency and performance. This section discusses the latest design innovations, including enhancements in micro-geometry and the development of customized tool solutions for specific manufacturing challenges. The impact of these innovations on manufacturing efficiency and productivity is highlighted, showcasing the continuous evolution of carbide cutting tools.
Sustainability and Recycling Efforts
The increasing emphasis on sustainability has brought the recycling of carbide tools to the forefront of industry considerations. This segment covers the importance of carbide recycling programs and the environmental benefits of reusing carbide materials. The challenges and solutions related to the sustainability of carbide cutting tools are also discussed, emphasizing the industry’s commitment to environmental responsibility.
Future Trends in Carbide Tools
The future of carbide cutting tools looks promising, with continuous innovations on the horizon. This section forecasts emerging trends, such as the application of nanotechnology in carbide tools and the development of smart tools that enhance connectivity and functionality. The potential impact of these future advancements on the manufacturing industry is explored, indicating a trajectory of ongoing improvement and innovation.
Challenges and Solutions
Despite their numerous advantages, carbide tools face challenges related to tool life and the machinability of materials. This part of the article addresses these challenges, offering insights into solutions and highlighting ongoing research aimed at extending tool life and improving performance across various materials.
The Role of Coatings in Performance Enhancement
Coatings are pivotal in extending the life and enhancing the performance of carbide cutting tools. This section investigates the various types of coatings used, such as TiN (Titanium Nitride) and AlTiN (Aluminum Titanium Nitride), and their benefits. The advantages of coated tools, including increased hardness, reduced friction, and improved wear resistance, are discussed in detail.
Case Studies of Successful Implementations
The effectiveness of carbide cutting tools is best illustrated through real-world applications. This segment presents case studies from the aerospace and automotive industries, where carbide tools have been instrumental in solving complex manufacturing problems. These examples provide tangible evidence of the benefits and versatility of carbide cutting tools in enhancing manufacturing outcomes.
Comparison with Other Cutting Materials
Comparing carbide tools with other cutting materials, such as high-speed steel (HSS), ceramics, and diamond cutting tools, offers valuable perspective on their relative advantages and applications. This comparative analysis sheds light on why carbide cutting tools are often the preferred choice for many manufacturing operations, due to their superior performance and durability.
Expert Opinions and Industry Insights
Incorporating expert opinions and industry insights enriches our understanding of the carbide cutting tool industry. This section features interviews with industry leaders and experts, offering their perspectives on current trends and future directions for carbide cutting tools. Their insights provide a deeper appreciation of the role and impact of carbide tools in modern manufacturing.
FAQs
Conclusion
The journey of carbide cutting tools from basic materials to the forefront of modern manufacturing is a remarkable story of technological advancement and innovation. As we have explored their evolution, types, applications, and the ongoing research and development, it’s clear that carbide cutting tools have fundamentally transformed manufacturing processes. Their impact on efficiency, precision, and sustainability continues to drive progress in the manufacturing industry, setting the stage for future advancements. With a commitment to innovation and sustainability, the future of carbide cutting tools in modern manufacturing looks brighter than ever.